
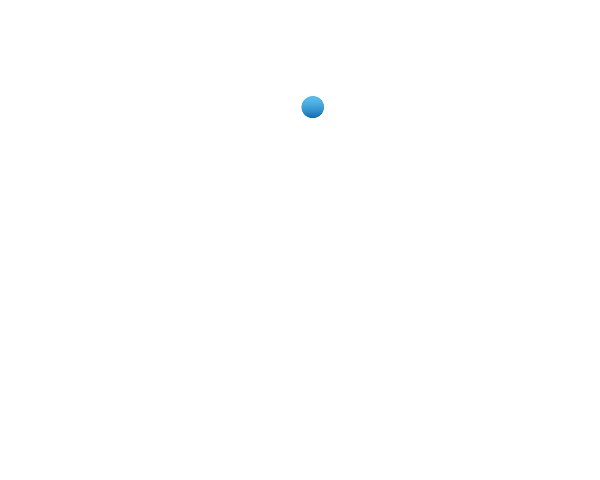

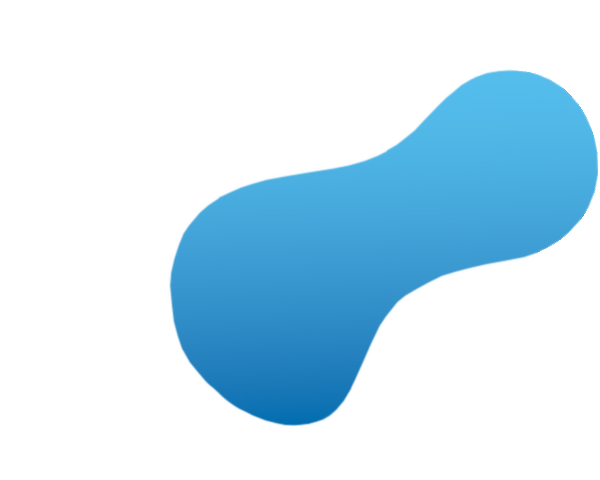

TWS
TWS - Washing Cabin Bin & Equipments
Construction Features
Depending on the function to be performed, the washing cabin can be constructed to lodge and wash bins on one hand, or simple equipment’s on the other hand. The two type’s can be modelled in two different machines or one execution can also accomodate the two functions.
The washing cabin comes in a “through the wall design”, in order to create a hermetic division between production area and clean area on the opposite site, which doesn’t come into contact according to all requirements needed in cleaning procedures. A flush floor installation is the perfect solution to load containers into the machine.
TWS is covered with a fully-welded AISI 304 fra- me and a internal chamber in AISI 316L with aninterior mirror polished finish (r.a. < 0.3 micron).The doors are provided with inflatable gaskets and large windows.
Functioning
- Pre-rinse with hot water
- Washing cycle with hot water (with water hea- ting ability and use of detergents)
- Rinse cycle with purified water (with the water heating option)
- Draining of the washing system and of the bin
- Drying and cooling of bin
TWS
TWS is an automatic washing and drying device designed and built to be installed in a pharmaceutical production area, according to the Good Manufacturing Practice criteria.
In the field of cleaning requirements, TAIM’s TWS washing system is specifically designed and is therefore very attractive in its realization and is applied to perform the cleaning of Bins for various types of shapes and sizes, for drums and various accessories used in the pharmaceutical departments to wash and dry internal and external surfaces of the same.

WASHING CABIN
The washing cabin is completely made of stainless steel and is formed with a recessed cleaning chamber in the partitions for clean rooms, with two doors.
A door leads to the dirty area and the second door on the other side overlooks the clean area, one in front of the other. According the present configuration, the bins that come from the area of use (dirty area) are loaded into the washing cabin, they are washed and discharged to the opposite side (clean area).
In addition, the doors are locked relatively according each other. If one door is open, the other cannot be opened. The doors are also equipped with a safety system to stop the washing cycle in case of an accidental opening of one of the doors.
In addition, the system is designed with the following precisions to be noticed:
- An external isolating panel
- Rounded corners to prevent injuries
- A grid to allows the positionning of the bin
- A tank for the recirculation of the rinsing water
- The washing sprayball for the cleaning procedures at the inside of the bin
- Side ramps with nozzles for external washing procedures of the bins
- Superior ramps with washing nozzles for internal washing procedures of the bins
- Inferior ramps with washing nozzles for washing procedures of the bins’ valves
- Two doors at 180° (dirty area/clean area) with closing system through an inflatable seal equipped with a safety system which allows to stop the washing cycle in case of an accidental opening of the door
- An air handling unit for internal and externaldrying of the bins (with f9 and then h13 filtersand differential pressure gauges for checking ofthe clogging of the filters)
The head will automatically switch from the top of the cabin into the bins to wash the inside. The outer parts of the bins are cleaned with other dedicated waterjets.
CIP System
TWS is equipped with a detergent system with automatic regulation of the dosage of the deter- gent. A full set of automatic valves which manages the washing phase in a completely automatic way. In addition also level detectors are installed to control the washing phases. Along the piping, instruments that guarantee complete control of all parameters are planned and installed. In addition, there is also a conductivity probe to monitor and ensure the reproducibility of the washing.
Analyzer : Conductivity probe
Although not necessarily required, but relying on our experience, a conductivity probe is provided, directly connected to the central processing unit that will allow each time to evaluate the succeeded operation of cleaning. Itself also contains a PT100 for corrections of the conductivity as a function of the sensed value. The conductivity value is then continuously monitored. The me-asuring range is 0-200 microSiemens/cm, theconnections to the process is of the sanitary type, triclamp. The signal is transmitted by an electric current, of the type 4..20mA.
Programmation of the Cycles
It is possible to configure the cleaning and drying cycles using the PC / PLC (recipe mode) and savethe programs in the system’s memory
Electricity outages
In case of power failure, the system is programmed so to protect the product against any risk of damage waiting for the resolution of the problem. The equipment stops automatically in a “safe” mode ensuring the continuity of the process.
Functionning & Process monitoring
The TWS’s software is conceived according the FDA CFR 21, part 11 regulations in a parametric, simple and intuitive application with GAMP guidelines, implemented with a SCADA functionality including process graphics with industrial standards. The software and hardware for the machine’s control system is created in-house. This results in a high degree of flexibility for personal requirements. The steps of washing are controlled using sensors. All information is viewed and recorded from the central unit development and is made available each time to the operator.
Security system
The system has an emergency stop device that can immediately stop the operation of the equipment needed. The emergency stop device is located in easily accessible areas, as required by safety standards. In addition, different types of alarms required, which provide audible and visual warning will be installed
Get Started
if you want more informations for our dynamic process, production flow and thecnologies, please contact us